Repair and restoration of parts
In sensitive and strategic industries where replacing a damaged part is not feasible, there is a greater preference for refurbishing and extending the lifespan of such components rather than replacing them. Today, various methods are employed for surface modification or restoration of industrial parts, each with its own advantages and disadvantages. For example, methods such as welding, particularly Tungsten Inert Gas (TIG) welding, and the modern Plasma Transferred Arc (PTA) welding technique, as well as thermal spray methods, including Atmospheric Plasma Spray (APS) and High-Velocity Oxygen Fuel (HVOF) spray, are commonly used.
Tungsten Inert Gas (TIG) welding
According to the American Welding Society (AWS), this process is also known as Gas Tungsten Arc Welding (GTAW). In this process, a non-consumable tungsten electrode or its alloys are used to transfer electricity between the workpiece and the electrode, creating an electric arc. In TIG welding, the molten pool is fully visible, and there is a risk of oxidation in the heated area and even the electrode. Therefore, to protect the molten pool from oxidizing and harmful atmospheric elements, inert gases are used. The most commonly used inert gas in this welding method is argon, which is why it is also referred to as argon welding. TIG welding can be performed with or without filler metal (welding wire). This method is applicable for a wide range of iron and non-iron metals in various thicknesses. Due to its many advantages, such as high welding quality, clean and precise welds, and the ability to weld thin sheets, argon welding has widespread applications in various industries.
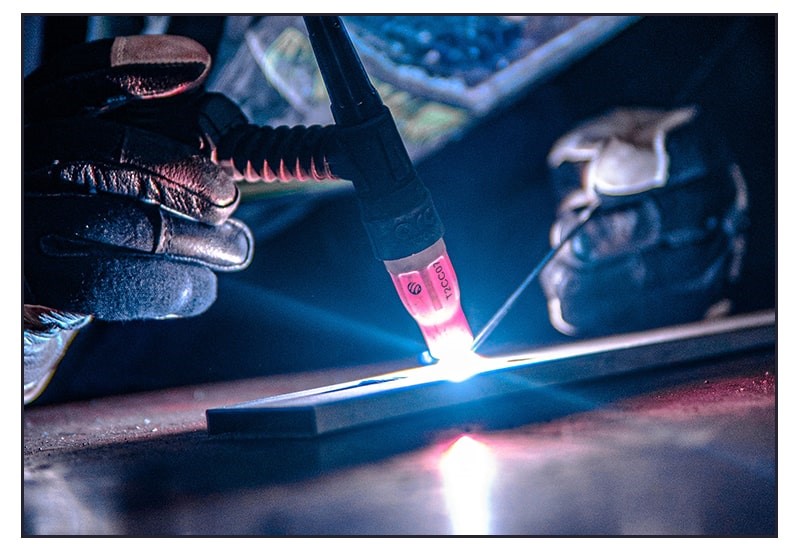
The Atmospheric Plasma Spray (APS) method
This method is one of the most widely used techniques in industry, suitable for creating high-quality refractory, coating-resistant, and corrosion-resistant Claddings . For example, it is used for Cladding various ceramics on rollers. The process operates as follows: the plasma gun consists of a water-cooled copper anode, a tungsten cathode, and a Cladding material nozzle.
Initially, a potential difference is established between the anode and the cathode. Then, the gas between the anode and cathode is ionized, and when electrical current is applied, the gas is heated intensely, causing it to expand. The gas exits the gun nozzle under pressure. If the Cladding material is in powder form, the powder particles are fed into the flame through the nozzle. If the material is in wire form, it is fed into the plasma area from the back of the gun with the help of several rollers.
Upon entering the plasma flame, the particles, depending on their size, are either melted or partially melted and impact the substrate surface at high velocity to form the Cladding. Ideal conditions are when the temperature of the particles on the surface is equal to their melting point.
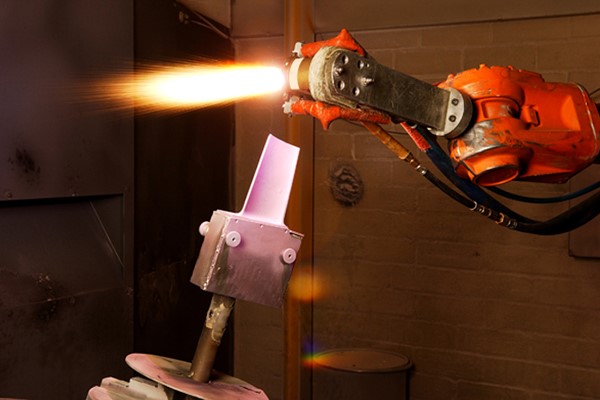
The High-Velocity Oxygen Fuel (HVOF) method
HVOF (High-Velocity Oxygen Fuel) Cladding have been used for over forty years for industrial applications to create hard and dense Cladding. In this process, oxygen is combined with various fuels such as hydrogen, propane, and kerosene. This method is one of the most advanced spray techniques, where fuel and oxygen are mixed in specific ratios and are expelled from the gun nozzle with high pressure and velocity after combustion.
Using the shockwave in the internal combustion chamber, carbide particles are applied to the surfaces of the target parts at speeds of approximately 1200 to 1500 meters per second. The energy from this reaction is expelled from the gun as heat and increased pressure, causing the powder to melt and accelerating the powder particles. Once the explosive conditions are stabilized, the powder is injected into the gun along with a neutral gas like nitrogen or argon, which acts as a powder carrier. The powder is accelerated and reaches the required speed due to continuous explosions.
The accelerated particles travel a very short distance to the opposite surface, which is positioned at an optimal distance, creating a completely smooth and resistant Cladding.
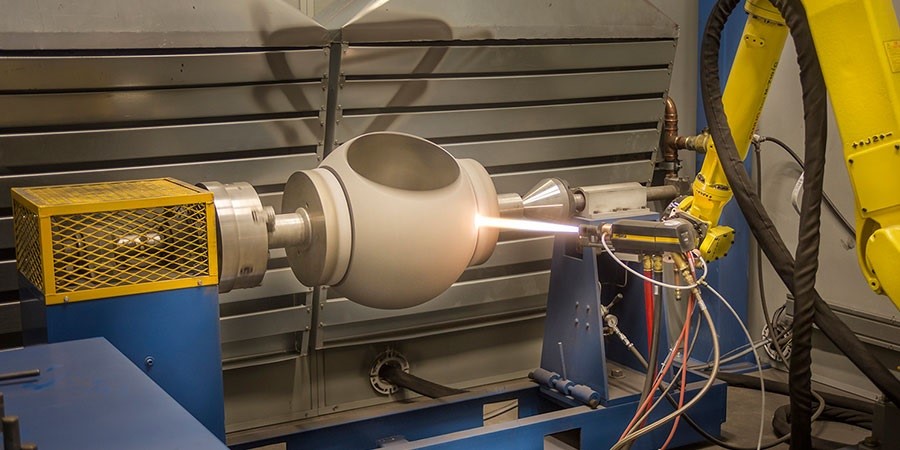
The modern Laser Cladding method
Among these methods, the use of high-energy beams, such as laser beams, offers capabilities far superior to traditional methods. Laser technology has been applied in various surface modification processes, yielding highly satisfactory results. Some of the issues with older methods include high porosity, poor adhesion to the substrate, and excessive heat application to the substrate, which can lead to microstructural disruption, warping, and, in some cases, even fracture of the component.
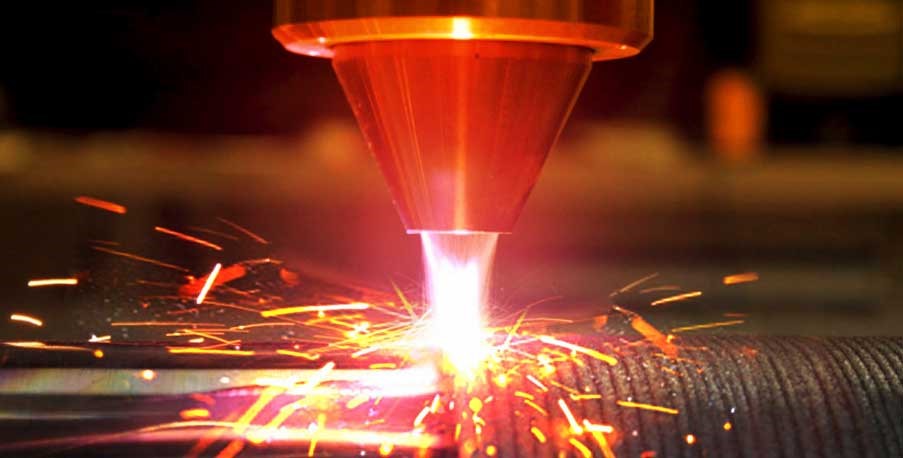
Laser surface processes offer high control in creating metallurgical structures tailored to the geometry and surface characteristics of components. These processes are relatively fast, resulting in a smaller heat-affected zone in the parts. As a result, they are considered a suitable method for Cladding and restoring industrial components. Consequently, laser cladding technology is regarded as an efficient process for the restoration of industrial parts. In this process, either an alloy identical to the substrate or an alloy with superior properties compared to the substrate is used to repair and improve the surface or damaged area.
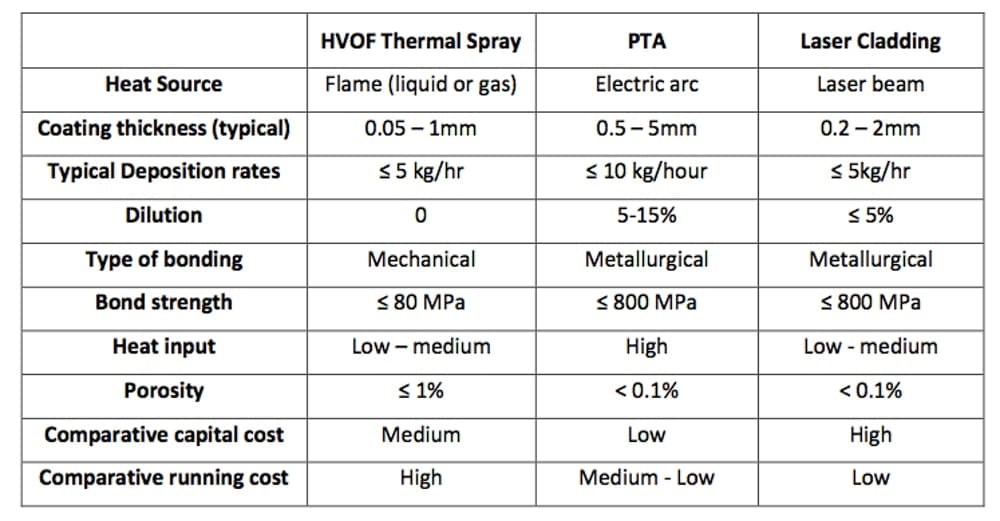
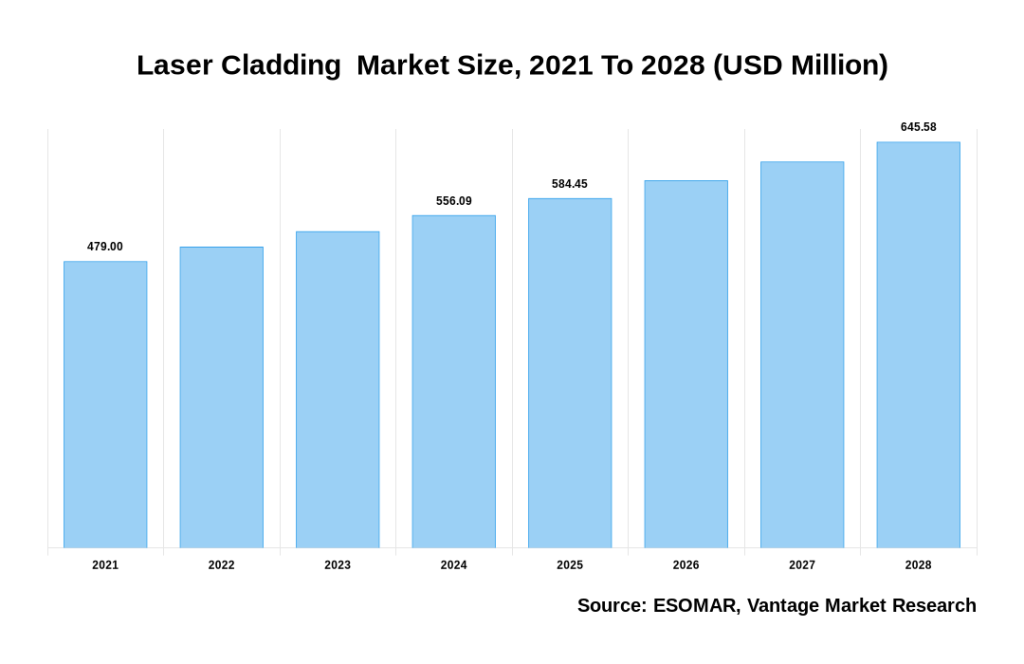
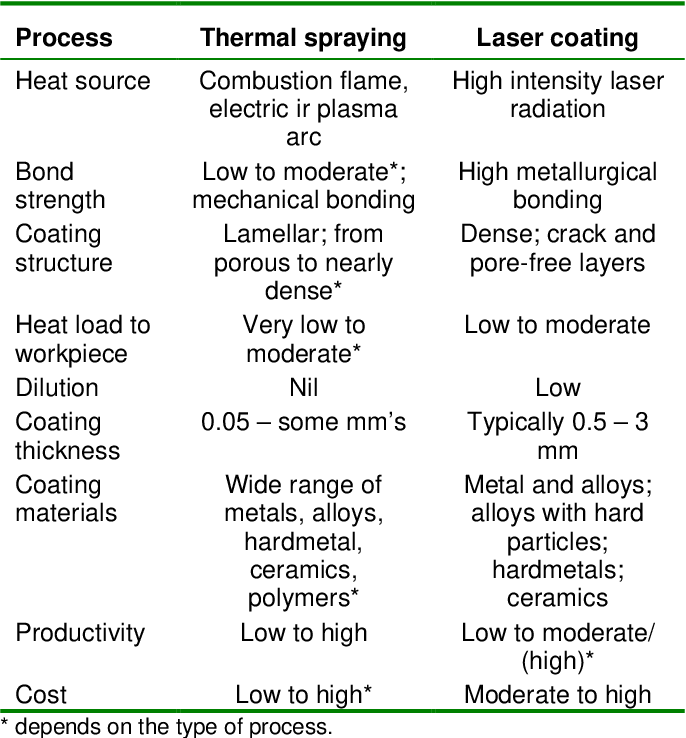