Why Laser Cladding(Laser Cladding)?
Laser Cladding, also known as “metal deposition using laser technology,” is an innovative technique for adding a material with desirable metallurgical, mechanical, and corrosion-resistant properties to the surface of another material. This process allows for the enhancement of a component’s surface characteristics, including resistance to various types of coating and corrosion, as well as the repair of damaged or worn surfaces.
In this technology, the metallurgical bond (weld) formed between the base material and the Cladding is considered one of the most precise and advanced welding processes available. Laser Cladding can be performed using powder materials (metal alloys, metal composites, superalloys) or wire (cold or hot wire). The laser source creates a molten pool on the surface of the workpiece, to which wire or powder is simultaneously added. Despite the high power of the laser source as a heat source, the time the laser beam is distributed over a cross-section of the component is short, resulting in rapid solidification and cooling. The outcome is the creation of a metallurgically sound Cladding.
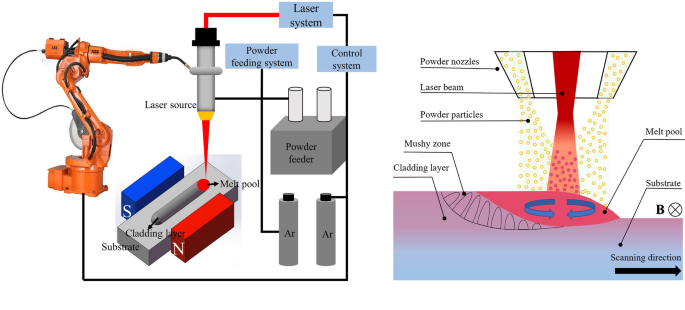
Laser Cladding produces a surface harder than what can be achieved with thermal spraying processes and presents significantly lower health risks compared to hard chrome plating processes.
In laser Cladding, it is possible to mix two or more powders and control the feed rate of each powder separately, making this process highly flexible. This means the process can be used for both the manufacturing and repair of components, allowing for the creation of different metal powders in each layer. Additionally, due to the localized fusion in the molten pool, material gradients at the microstructural level can be designed, allowing the coated materials to be tailored for specific applications.
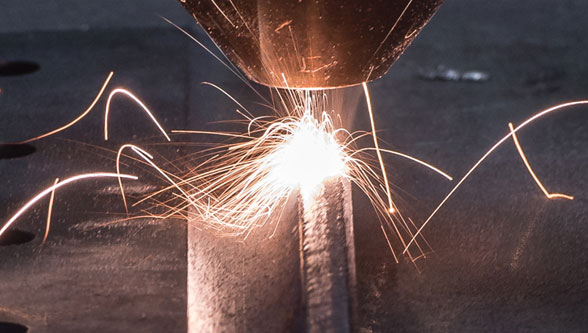
The laser Cladding process offers several advantages compared to conventional Cladding methods. Some of the key benefits include:
- Precision Application: The ability to apply the Cladding exactly where needed on the component.
- Material Flexibility: A wide selection of metal powders and substrates (target parts) for alloying or producing metal and ceramic matrix composites (MMC).
- Low Porosity: A process that results in low or even zero porosity in the deposits on the component (density over 99.9%).
- Minimal Heat Input: Relatively low heat input to the component, resulting in a narrow heat-affected zone (HAZ) (in high-speed Cladding processes, the HAZ width can be less than 10 microns).
- No Warping or Distortion: The process avoids warping or distortion of the component.
- Surface Uniformity: Provides a homogeneous and smooth surface, reducing the need for additional machining.
- Easy Automation: Simple to automate and integrate into CAD/CAM software environments.
- Shorter Processing Time: Much shorter processing time compared to conventional methods.
- Automated Thermal Control: Full automatic and online thermal control through laser power modulation.
- Versatile Production: Ability to produce parts with different grades and unidirectional grain structures.
- Accurate Deposition Rate: Precise and measurable deposition rates.
- Enhanced Mechanical Properties: Improved mechanical properties compared to the base metal.
- Effective for Repair: Suitable for repairing worn-out and out-of-service components.