چرا پوشش دهی با لیزر (لیزر کلدینگ)
روکش کاری لیزری که به عنوان “رسوب فلزی به کمک فناوری لیزر” نیز شناخته می شود، تکنیکی نوین برای افزودن یک ماده با خواص متالورژیکی، مکانیکی و خوردگی مطلوب به سطح ماده دیگر است. در این فرآیند امکان بهبود ویژگی های سطح یک قطعه از جمله مقاومت در برابر انواع سایش، خوردگی و همچنین امکان ترمیم سطوح آسیب دیده یا فرسوده فراهم است. در این فناوری، پیوند متالورژیکی (جوش) حاصله بین ماده پایه و روکش، یکی از دقیق ترین و جدیدترین فرآیندهای جوشکاری در دسترس به شمار می آید. روکش کاری لیزری را می توان با استفاده مواد اولیه پودری (آلیاژهای فلزی، کامپوزیت های فلزی، سوپرآلیاژ) و یا سیم (سیم سرد یا گرم) انجام داد. منبع لیزر یک حوضچه مذاب روی سطح قطعه کار ایجاد می کند که همزمان سیم یا پودر به آن اضافه می شود. علیرغم قدرت بالای منبع لیزر به عنوان منبع گرما، زمان توزیع اشعه ی لیزر بر یک سطح مقطع از قطعه کوتاه است و این بدان معنی است که زمان انجماد و سرد شدن سریع است. نتیجه این امر، ایجاد یک روکشِ بالک متالورژیکی است.
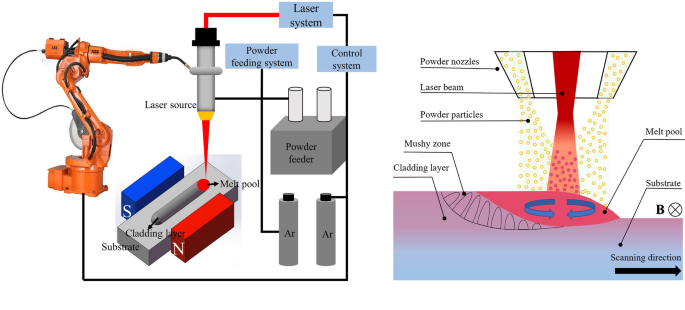
که سخت تر از آن چیزی است که می توان با فرایند پاشش حرارتی به دست آورد و نسبت به فرآیند آبکاری سخت کروم از نظر سلامتی خطر به مراتب کمتری دارد.
در فرایند روکشکاری لیزری امکان مخلوط کردن دو یا چند پودر و کنترل نرخ پودر برای هر دو به طور جداگانه وجود دارد و به این بدان معنی است که این فرآیند یک فرایند کاملاً انعطافپذیر است و میتوان از این فرایند برای ساخت و تعمیر قطعات با امکان ایجاد جنس های مختلف از پودر فلزات در هر لایه استفاده کرد. علاوه بر این، به دلیل همجوشی موضعی در حوضچه مذاب این امکان وجود دارد تا گرادیان مواد در سطح ریزساختاری طراحی شود، لذا مواد روکشکاری شده میتوانند در کاربردهای خاص استفاده شوند.
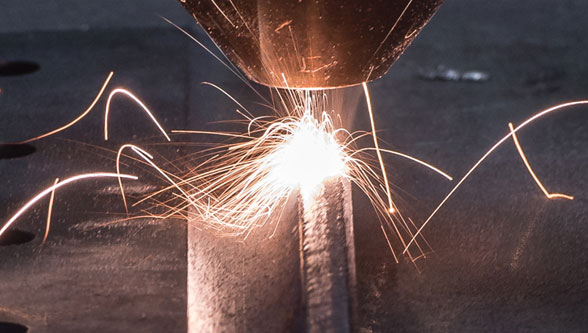
فرایند روکش کاری لیزری در مقایسه با فرآیندهای معمولی پوشش دهی مزایای متعددی دارد. از مزایای فرایند روکش کاری لیزری می توان به ایجاد لایه پوششی با کیفیت بالاتر (از جمله استحکام و یکپارچگی بالاتر) با اعوجاج و رقت بسیار کم و همچنین افزایش کیفیت سطح اشاره کرد. این مزایا عبارتند از :
- امکان ایجاد پوشش دقیقاً در جایی از قطعه که مورد نیاز است.
- امکان انتخاب گسترده از بین انواع پودرهای فلزی و زیرلایه ها (قطعه هدف) به منظور آلیاژسازی یا تولید مواد کامپوزیتی فلزی و سرامیکی (MMC).
- فرایندی با تخلخل کم یا حتی بدون تخلخل در رسوبات ایجاد شده بر روی قطعه (چگالی بیش از 99.9%).
- گرمای ورودی نسبتاً کم به قطعه، منجر به ایجاد یک منطقه تحت تأثیر حرارت (HAZ) باریک می شود (در فرایند روکش کاری از نوع سرعت بالا، عرض ناحیه HAZ به کمتر از 10 میکرون هم می رسد).
- بدون ایجاد تاب و اعوجاج در قطعه.
- همگنی و صافی سطح مطلوب که در نتیجه به ماشینکاری محدودی نیاز است.
- اتوماسیون آسان و ادغام در محیط های نرم افزاری CAD/CAM.
- زمان اجرا در فرایند روکش کاری لیزری نسبت به روش های معمولی بسیار کمتر است.
- امکان کنترل حرارتی تمام اتوماتیک و به صورت آنلاین در زمان اجرا، به واسطه تغییر مدولاسیون توان لیزر.
- امکان تولید قطعات با گریدهای متفاوت و ساختارهای یک جهته در رشد دانه.
- نرخ رسوب دقیق و قابل اندازه گیری.
- خواص مکانیکی مطلوب تر از فلز پایه.
- فرایندی مناسب برای تعمیر قطعات فرسوده و خارج شده از چرخه ی کاری.