تعمیر و بازسازی قطعات
در صنایع حساس و استراتژیک که امکان جایگزینی قطعه تخریب شده وجود ندارد، تمایل صنایع به بازسازی و افزایش طول عمر اینگونه قطعات نسبت به جایگزینی آنها بیشتر است. امروزه روشهای مختلفی به منظور اصلاحسازی سطحی یا بازسازی قطعات صنعتی بکار گرفته شده که هرکدام از مزایا و معایبی برخوردارند. به عنوان مثال می توان از روشهای جوشکاری، به خصوص روش جوشکاری تنگستن با گاز خنثی TIG و روش نوین جوشکاری تحت عنوان جوشکاری قوس انتقالی پلاسما PTA و همچنین روشهای پاشش حرارتی Thermal Spray، بخصوص روش پاشش پلاسمایی APS و روش پاشش شعله ای با سوخت و اکسیژن با سرعت زیاد HVOF نام برد.
روش جوشکاری تنگستن با گاز خنثی TIG
براساس نامگذاری انجمن جوشکاری آمریکا، AWS، با نام جوشکاری GTAW نیز کاربرد دارد. در این فرایند، از یک الکترود غیرمصرفی از جنس تنگستن یا آلیاژهای آن، برای انتقال جریان الکتریسیته بین قطعه کار و الکترود و ایجاد قوس الکتریکی، استفاده میشود. در جوشکاری TIG، حوضچه مذاب کاملا قابل مشاهده است و احتمال اکسیدشدن منطقه تحت حرارت و حتی الکترود، وجود دارد. بنابراین به منظور حفاظت از حوضچه مذاب در مقابل عناصر اکسیدکننده و مخرب اتمسفر، از گازهای خنثی استفاده میشود. متداولترین گاز خنثی مورد استفاده در این روش جوشکاری، آرگون است. به همین دلیل، به آن جوشکاری آرگون نیز گفته میشود. جوشکاری تیگ آرگون به هر دو صورت با فلز پرکننده (سیم جوش) و یا بدون فلز پرکننده قابل انجام شدن است. این روش برای انواع فلزات آهنی و غیرآهنی در محدوده گستردهای از ضخامتها کاربرد دارد. جوش آرگون به دلیل مزایای بسیاری که دارد مانند کیفیت جوشکاری بالا، ایجاد جوش تمیز و ظریف و امکان جوش دادن ورقهای نازک، کاربرد گستردهای در صنایع مختلف دارد.
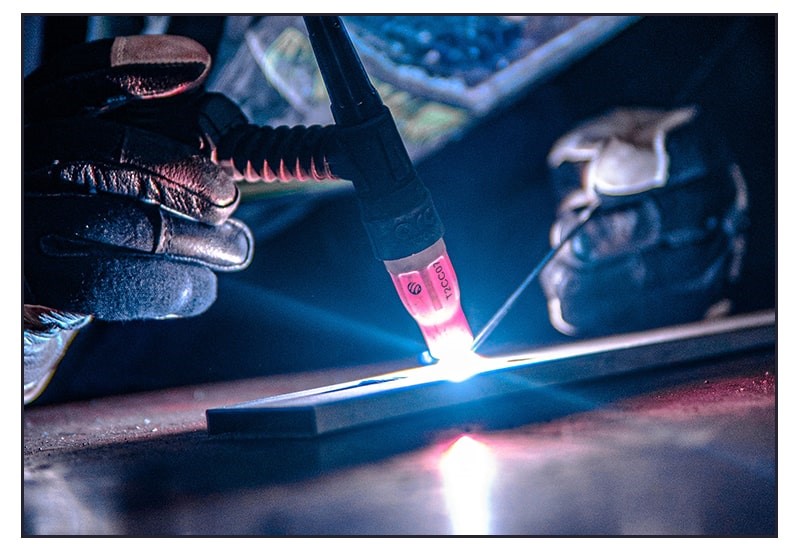
روش پاشش پلاسمایی APS
این روش از پراستفادهترین روشها در صنعت میباشد که روش مناسب برای ایجاد پوششهای دیرگداز و مقاوم به سایش و خوردگی با کیفیتی مناسب است و به عنوان نمونه از آن برای پوششدهی انواع سرامیکها بر روی غلطکها استفاده میگردد و عملکرد آن به این صورت است که تفنگ پلاسمایی متشکل از یک آند مسی به صورت آبگرد و یک کاتد تنگستنی و نازل مواد پوشان میباشد. طرز کار به این صورت است که ابتدا اختلاف پتانسیلی بین آند و کاتد برقرار شده و سپس گاز بین آند و کاتد یونیزه شده و با برقراری جریان برق گاز به شدت گرم میگردد و حجم آن اضافه میشود. در این حال گاز با فشار از دهانه تفنگ خارج شده که اگر ماده پوشان به صورت پودر باشد ذرات ماده پوشان در دهانه خروجی تفنگ به درون شعله تغذیه میگردد و اگر به صورت سیم باشد از عقب تفنگ و به کمک چند غلطک وارد قسمت پلاسما میگردد. با ورود ذرات به درون شعله پلاسما این ذرات بر حسب اندازهای که دارند، ذوب و یا نیمه مذاب میشوند و با سرعت بر روی سطح زیرلایه برخورد میکنند تا پوشش تشکیل شود. شرایط ایدهآل شرایطی است که دمای ذرات بر روی سطح برابر نقطه ذوب آنها باشد.
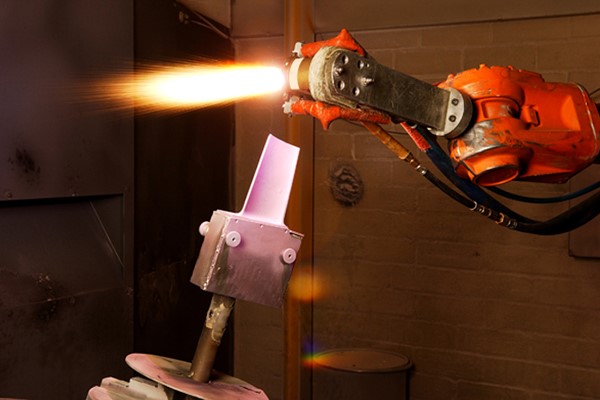
روش HVOF
پوشش های HVOF بیش از چهل سال است که به منظور کاربردهای صنعتی و ایجاد پوشش هایی سخت و چگال بکار رفتهاند. در این فرآیند از ترکیب اکسیژن با انواع مختلفی از سوخت ها مانند هیدروژن، پروپان و کاروسین استفاده می نماید. این روش یکی از پیشرفته ترین روش های اسپری است که در آن سوخت و اکسیژن با نسبت خاصی باهم مخلوط شده و پس از احتراق با فشار و سرعت زیادی از دهانه تفنگ خارج میشوند. با استفاده از موج انفجار در محفظه احتراق داخلی ، ذرات مواد کاربیدی با سرعت حدود ۱۲۰۰ تا ۱۵۰۰ متر بر ثانیه بر روی سطوح قطعات مورد نظر اعمال می شوند. انرژی حاصل از این واکنش به صورت حرارت و افزایش فشار از تفنگ تخلیه می گردد که باعث ذوب شدن پودر و سرعت دادن به ذرات پودر می شود. پس از تثبیت شرایط انفجاری، پودر با یک نرخ کنترل شده به همراه یک گاز خنثی مثل نیتروژن یا آرگون که نقش حامل پودر را دارد، توسط یک دستگاه تزریق پودر وارد تفنگ می شود و به همراه گازهای محترقه در اثر انفجارهای مداوم شتاب می گیرد و به سرعت لازم می رسد. این ذرات شتاب داده شده در زمانی بسیار کوتاه به سطح مقابل که در یک فاصله بهینه قرار دارد میرسند و سطحی کاملاً صاف و مقاوم را ایجاد می کند.
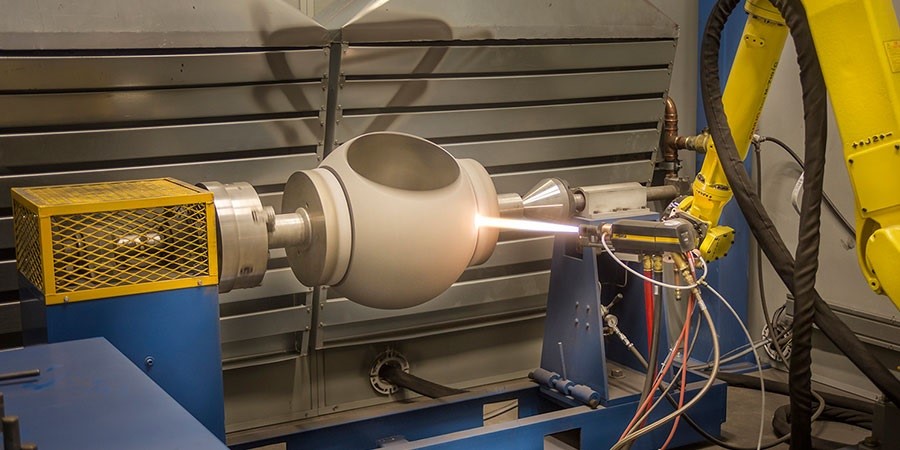
روش نوین لیزر کلدینگ
در این بین روشها استفاده از پرتوهای پرانرژی نظیر پرتو لیزر از قابلیتهای به مراتب بیشتری نسبت به روشهای مرسوم برخوردار است. استفاده از لیزر در انواع اصلاحسازیهای سطحی بکار گرفته شده و نتایج بسیار مطلوبی نیز بدست آمده است. از جمله معضلات موجود در روش های قدیمی، می توان به تخلخل بالا، چسبندگی نامناسب با زیرلایه و اعمال حرارت زیاد به زیرلایه اشاره نمود که باعث بههمریختگی ساختار میکروسکوپی، اعوجاج و نهایتاً در برخی موارد موجب شکستگی قطعه میشود.
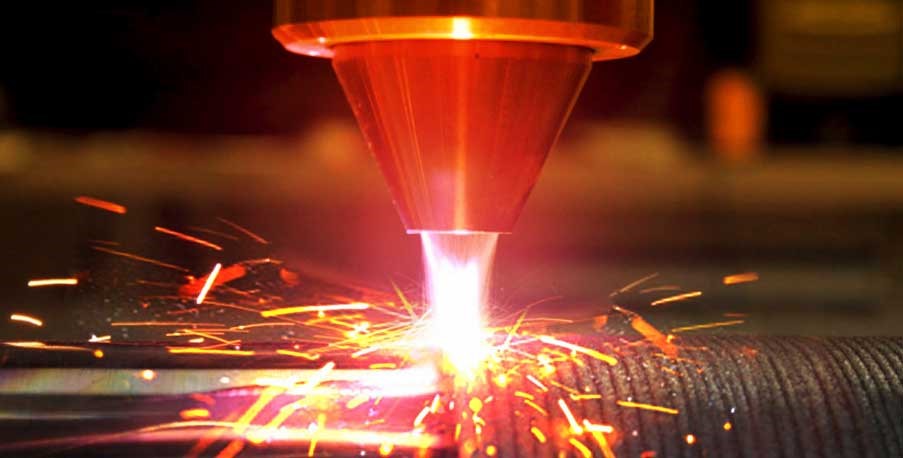
فرایندهای سطحی لیزری از کنترل پذیری بالاتری در ایجاد ساختارهای متالورژیکی با توجه به هندسه و ویژگی های سطحی قطعات برخوردار است. سرعت این فرایند نسبتا زیاد بوده و از اینرو منطقه متاثر از حرارت کمتری در قطعات ایجاد میکند. بنابراین بهعنوان روشی مناسب برای پوششدهی و بازسازی قطعات صنعتی مورد توجه واقعشده است. بالطبع فناوری لیزر کلدینگ نیز از فرایندهای پربازده در زمینه بازسازی قطعات صنعتی بهشمار خواهد رفت. در این فرایند از یک آلیاژ هم جنس زیرلایه معیوب یا از آلیاژی با خواص بهتر نسبت به زیرلایه به منظور اصلاح و بهسازی سطح یا منطقه معیوب استفاده می شود.
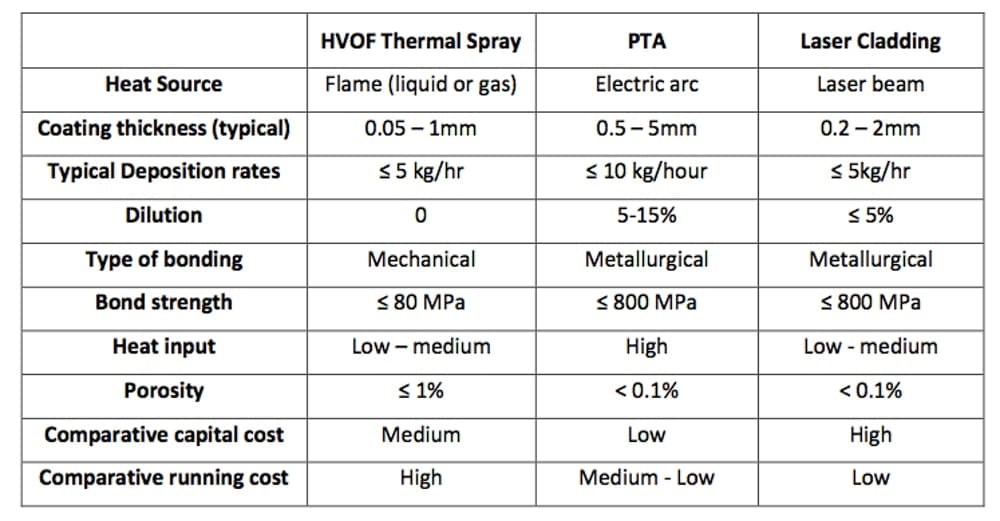
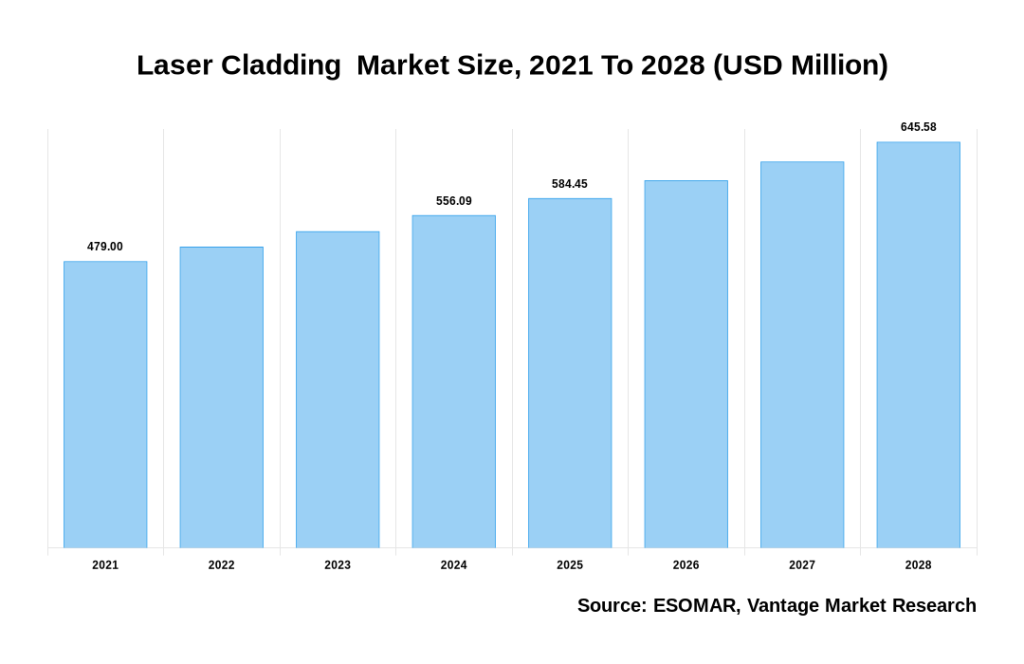
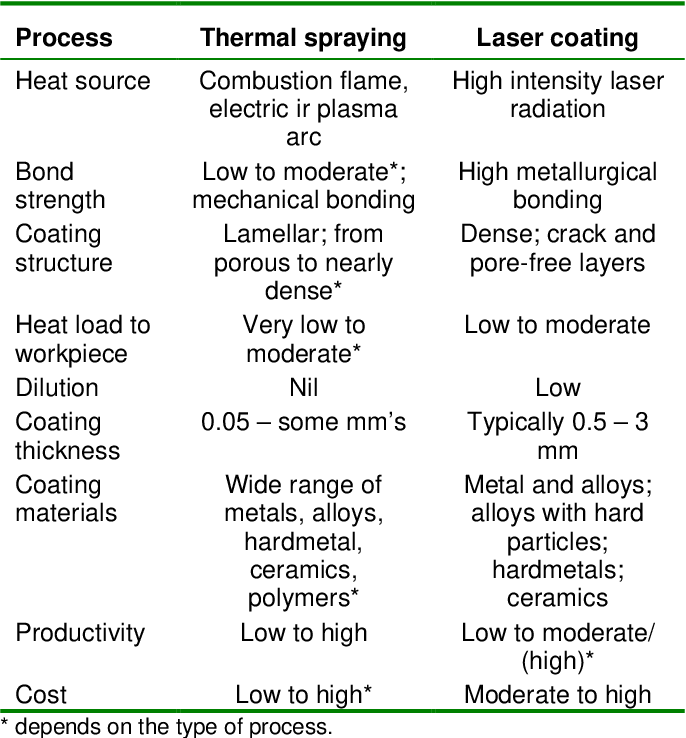